When repairing and installing floor joints without the guidance of architectural specifications or engineering drawings it may be tempting to disregard the need for proper joint care. However, not preparing the joints for the stresses it has to endure is a penny-wise pound-foolish approach that will almost surely result in floor failure.
As a solutions-driven company, we take the time to understand the mechanical, chemical, and/or thermal loads our clients’ floors will experience, so we can install the appropriate joint solution.
Mechanical loads
The impact of mechanical loads on the floor joints is often more onerous than the stress placed on the floor itself. For floors exposed the mechanical loads, we recommend our specialist joint system that has a shore hardness of A75-78, the joint is 8-12mm wide and is installed at a depth of 20-25mm. In addition, we install a 40mm angle iron that is embedded in the screed, effectively transferring the impact load onto the screed which has a higher capacity to absorb loads.
Thermal loads
In production facilities where high thermal shock is experienced, we install a 10mm polystyrene board at the full depth of the slab but remove 10-15mm of the board at the finished floor level to allow for the installation of an oversized polyurethane backing cord. We then prime the recess and inject a soft joint with a shore hardness of A30-36 to the finished floor level. This joint system can withstand high thermal shock from negative 40°C to 265°C.
Chemical loads
As each chemical load, based on its chemical composition, concentration and temperature will require a unique solution we are not able to cover all the various solutions in this post. To recommend an appropriate solution we will start by requesting the following:
- Function of the proposed installation area,
- MSDS documents for the chemicals to be used,
- The anticipated concentration of the chemicals
- How long discharges will remain on the floor and
- What colour has been specified for the area.
Once we understand these elements we will be able to specify an appropriate joint system.
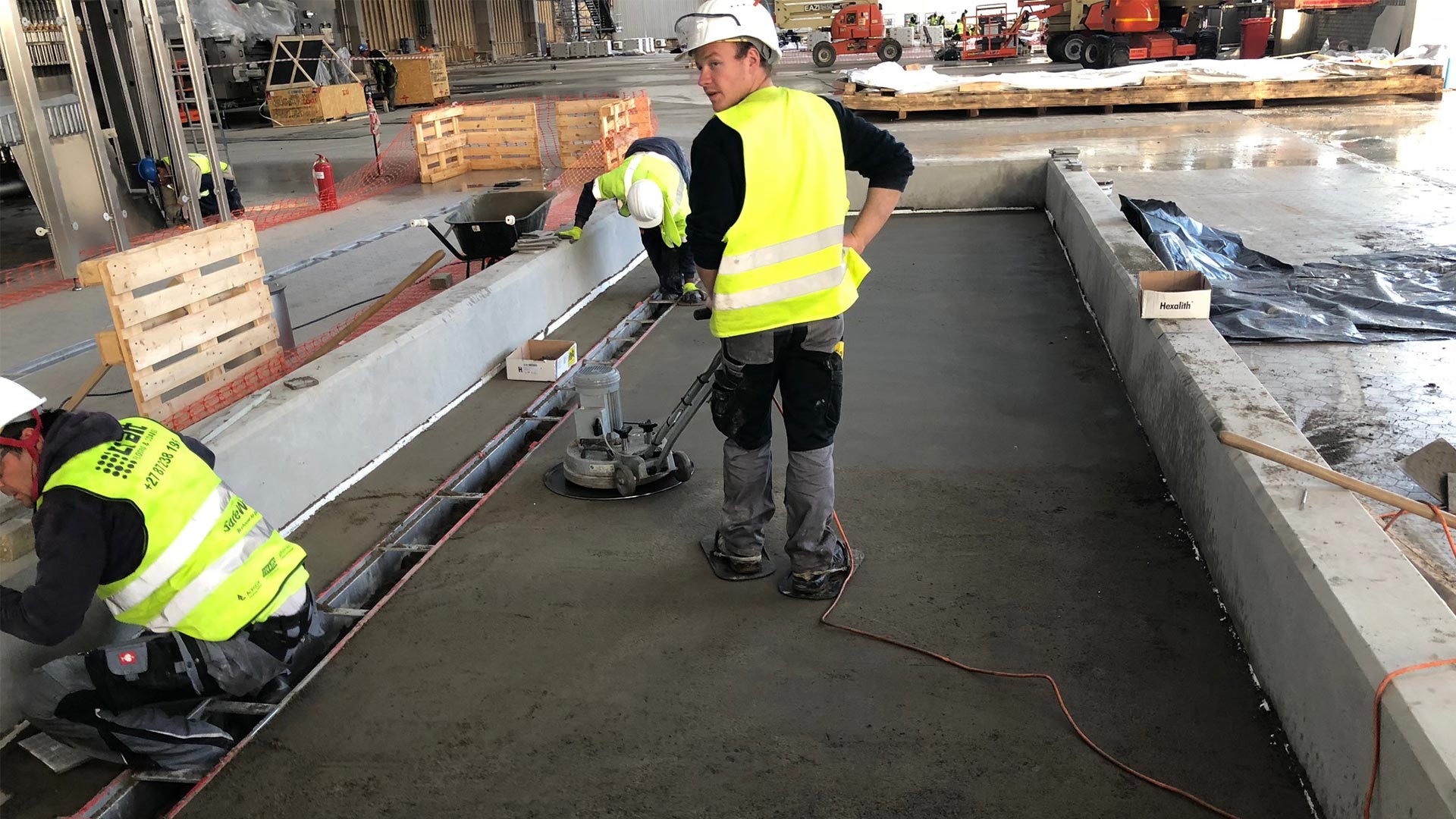
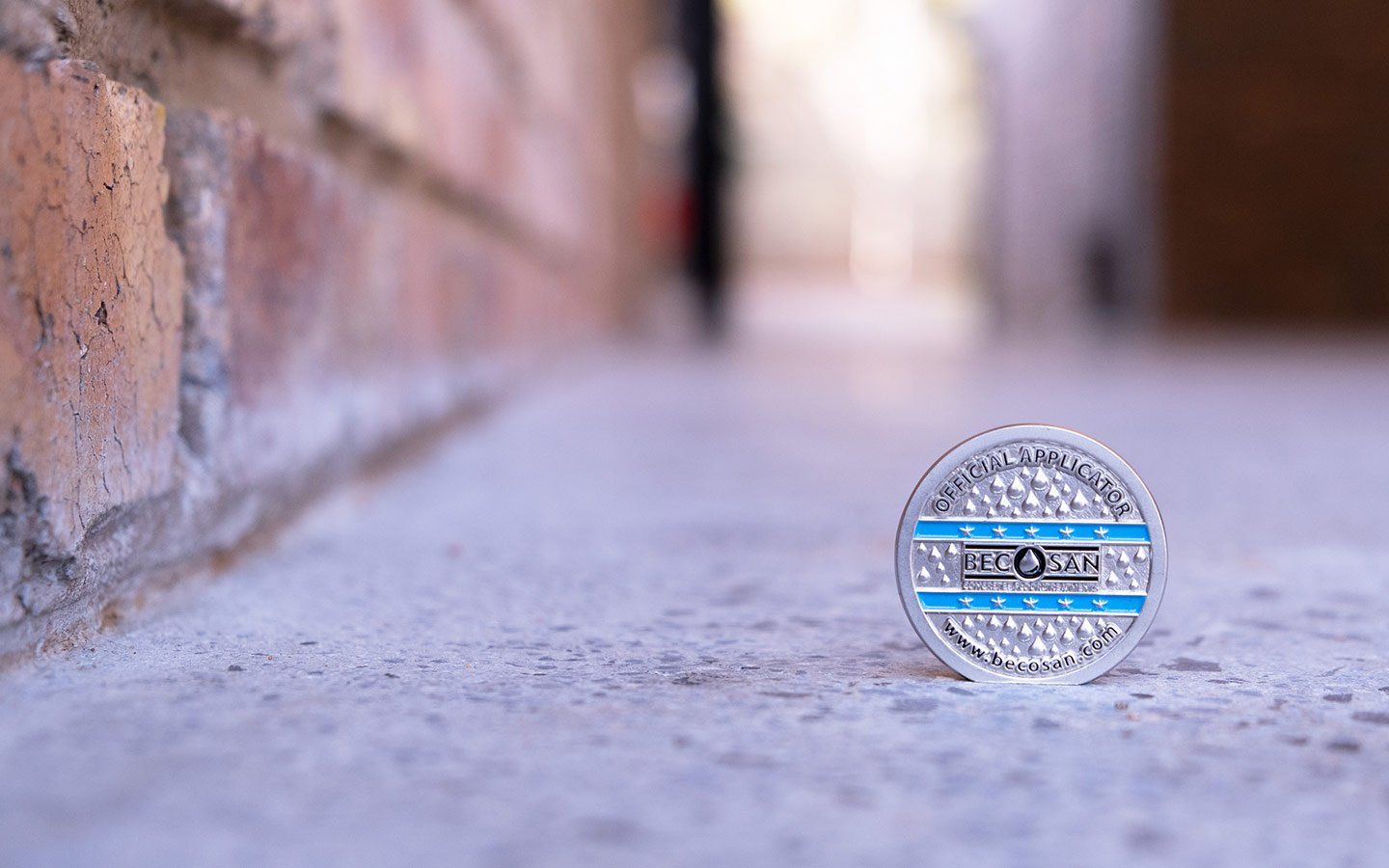