Commercial and manufacturing facilities understand the need for a well-designed, hygienic, durable, adaptable, cleanable, and serviceable drain system. Working closely with the engineering and production teams we can design a suitable full-service drain solution, commission the manufacture thereof, and then install the system in line with the specified requirements.
In addition to the drain system, we can also design and install specialist chemical and cementitious screeds, heavy industrial coatings, and industrial tiling systems to give a superior finish to the drain installation. All our solutions are underpinned by a warranty of up to ten years and as the supplier and installer of our products, there are no arguments about split responsibilities in the unlikely event that there is a problem with the installation.
Sustainable design
Designing a suitable drain system requires thorough knowledge of the project and/or facility. Below is a list of the elements that drive the design of a drainage solution. All the components must be considered in concert to achieve a workable drainage system.
- Viscosity – The consistency of the substance being discharged directly or indirectly into the drain system.
- Temperature – The temperature of the media affects the viscosity and flow rate of the material.
- Velocity – The volume of material discharged into the drain system at any time must be drained out as quickly as possible.
- Floor flow rates – Any material discharge onto the production floor must be drained into the drain in the shortest possible time.
- Floor panel size – Panels must be designed to contain any indirect discharge in designated areas to limit the potential for cross-contamination.
- Flow restriction points – When assessing potential restriction points, the number of drain openings is a key consideration.
Protecting transition areas
It is the transition area between the floor drain and the floor protection system that is most susceptible to failure. The mass material that surrounds and anchors the drain must be specified to address the loading capacity, a point that is unfortunately often overlooked.
To extend the life-cycle of the drain we recommend placing a durable, high-strength chemical mortar infill in the drain recess to support the drain’s dynamic loading capability. The drain grid must be designed to withstand the impact of materials handling equipment and fabricated with appropriate grade stainless steel so it does not bend or buckle. The drain’s load handing capacity can be further improved by reinforcing the drain profile with stainless steel tubing to mitigate the stress of tensile surface bed movement.
Choose your stainless steel with purpose in mind
The choice of stainless steel for a drain system design is ultimately driven by the mechanical and chemical loads it is expected to carry. While mechanical load will dictate the thickness of the stainless steel, the chemical load will determine the appropriate grade of stainless steel.
To deliver a sustainable long-term drainage system the metallurgist charged with specifying the wall thickness of the effluent system must also consider the chemical and thermal loading capacity of the drain.
The most common stainless steel grades used in drain design are as follows:
- AISI 304L is the most versatile grade of stainless steel and a popular go-to for stainless steel projects. As a low-carbon stainless steel, as indicated by the ‘L’, it can withstand normal clean-in-process temperatures and chemicals.
- AISI 316L is also a low-carbon stainless steel and is well-suited to particularly corrosive and high-temperature environments.
Maintaining drain hygiene
Over the years we have designed and installed drain systems for the food and beverage sector, pharmaceutical manufacturers, retail outlets, and commercial facilities. Our advice is to plan for the long term. In fact, we would encourage engineers to over-specify underground drains to accommodate future production or capacity expansion. Updating a drain system is a costly and disruptive exercise; absorbing the cost of over-specification now could save money and avoid many headaches in the long run.
An optimally designed drain will self-clean to maintain its flow capabilities, with well-designed access points (manholes, hatches, and rodding eyes) that make it easy to flush out any blockages, contributing to the hygiene of the facility and limiting production downtime. If your organisation is green-minded it is worthwhile considering environmentally friendly drains that require significantly less water to flush out solids.
Effluent piping – The backbone of all drain systems!
As manufacturing technology becomes more advanced and equipment manufacturers are able to double or even triple their manufacturing capacity using the same amount of space used ten years earlier, it is important to be forward-thinking when designing effluent pipes. A drain system designed with a 20-to-30-year horizon will substantially reduce manufacturing, maintenance, safety, and hygiene costs over the lifecycle of your asset.
In our experience material failures are often the result of chemical erosion and abrasion within the effluent drain system. Investing in the appropriate grade of steel for your environment at the outset, while it may appear more costly in the short term, it will save you in the long run.
In conclusion
Consult a qualified, experienced engineer and seek advice from drain manufactures who have much input to offer. A clever design that anticipates all the pain points and accommodates easy access maintenance and cleaning points with well-placed rodding eyes and manhole covers will mitigate expensive maintenance and future plant engineers will surely thank you for it.
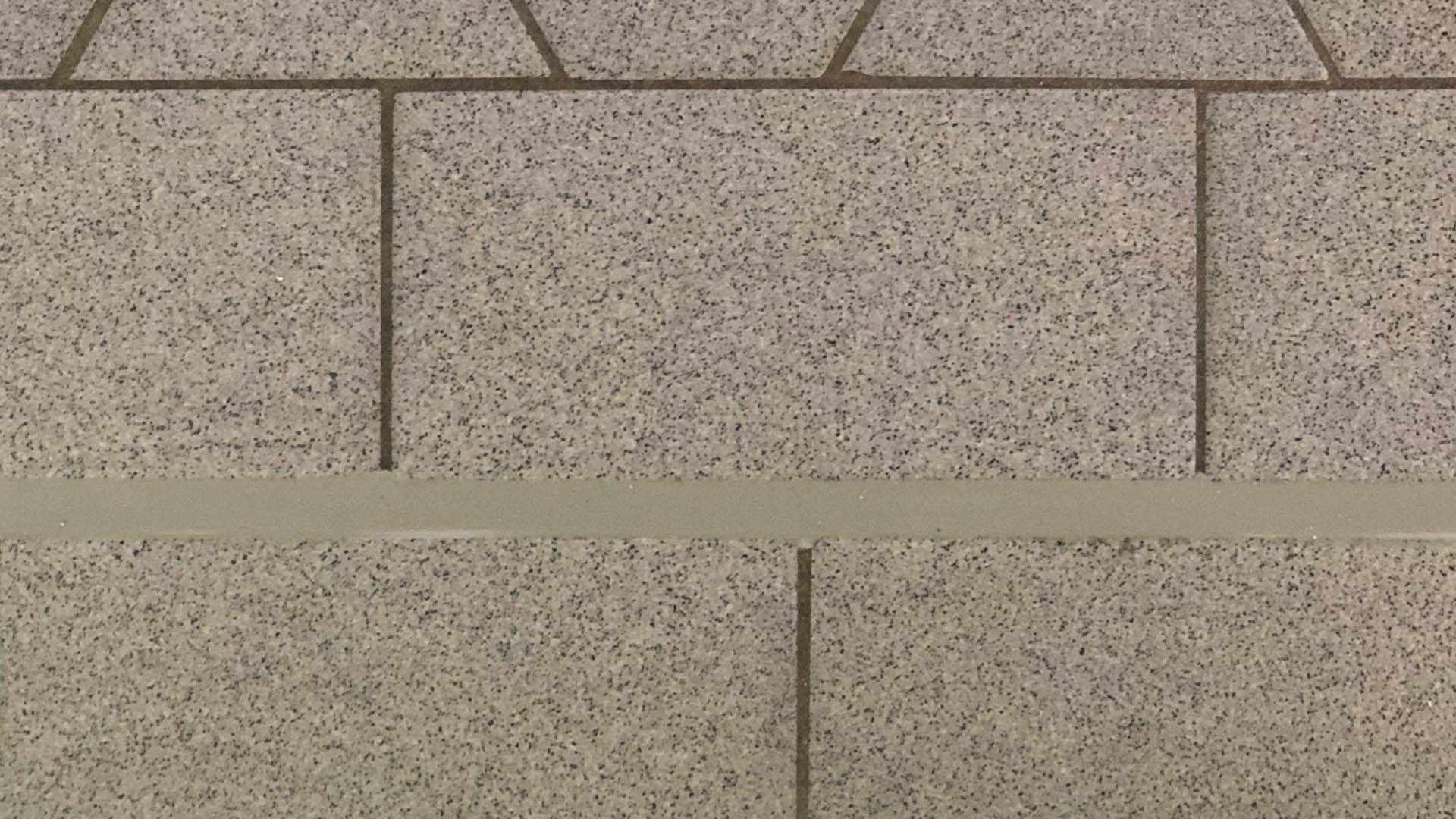
When repairing and installing floor joints without the guidance of architectural specifications or engineering drawings it may be tempting to disregard the need for proper joint care. However, not preparing the joints for the stresses it has to endure is a penny-wise pound-foolish approach that will almost surely result in floor failure.
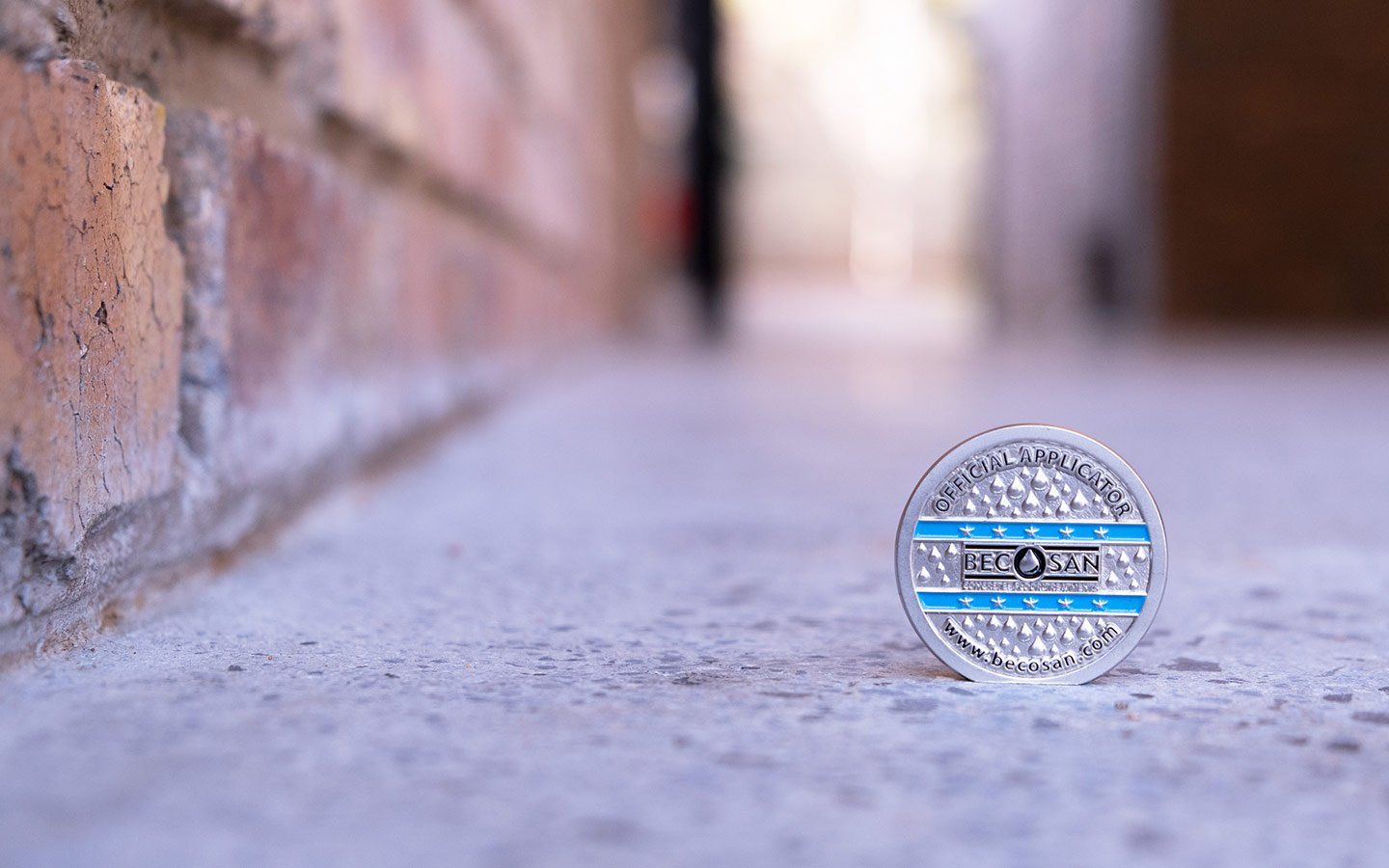
Craft Flooring & Coatings was approached by the owner of Venue 466 to assist with an unsightly delaminating floor covered with an epoxy coating that offered very little slip resistance. By treating the floor with Becosan’s non-film forming treatment the facility now boasts a beautiful non-slip, low maintenance concrete floor that will not delaminate.