One of the most significant elements to understanding the value of modified methyl methacrylate flooring is appreciating the difference between set time and full chemical cure.
Set time is defined as the time it takes for the product to become viable, while full chemical cure time is the period required for the product to realise its minimum, innate operational properties, i.e. the point at which it offers full mechanical, chemical- and thermal load resistance.
TIME IS OF THE ESSENCE
For traditional reactive resin coatings, like epoxy and polyurethane (PU), the set time between layers is typically 12 to 48 hours at 20⁰C. Achieving a full chemical cure requires a minimum of five, but up to 21 days depending on the system. Clients, however, are rarely informed about the need to allow the coating to achieve a full chemical cure; instead, as soon as the set time has lapsed it is business as usual with the floor being exposed to water, chemical- and/or mechanical loads that will invariably cause the coating to fail prematurely.
Modified methyl methacrylate (M-MMA) technology, as it applies to floor coatings, has been developed and proven over the past 35 years, and has been formulated to address many of the problems inherent in traditional reactive resin coatings, including much quicker curing times.
ARE YOU COMPARING APPLES WITH APPLES?
Epoxy coatings:
It takes an epoxy floor coating at least 21 days to achieve a full chemical cure. Achieving an optimum cured state requires a mean average ambient temperature of between 30°C and 50°C, and humidity levels that do not exceed 80%. At temperatures lower than 30°C, which would hold true for most operating areas, there is a risk that a measure of the epoxy monomer may not fully cure and the resultant epoxy dust generated by normal wear presents a possible health hazard. In addition, if the epoxy is not fully cured, any water contact within the first week will stain the floor and increase the potential for failure.
Polyurethane coatings:
Polyurethane coatings will achieve a full chemical cure in five to seven days. As with epoxy, the curing time is adversely affected by a relative humidity exceeding 80% and, depending on the brand, an ambient temperature lower than 10°C.
Most local data sheets recommend full traffic and moisture exposure only be permitted after 48 hours. This recommendation, however, assumes an ambient temperature of 30°C with a relative humidity of 50% when, in reality, most facilities operate in ambient temperatures lower than 30°C, and in beverage or similar processing plants the relative humidity is typically higher than 80%.
Modified methyl methacrylate coatings:
All M-MMA and MMA coatings achieve a full chemical cure in only two hours, even at temperatures as low as minus 25°C, and regardless of the relative humidity value. The ability of M-MMA coatings to cure in sub-zero temperatures mean that rapid project turnaround can even be achieved in a fridge or next to freezers.
By opting for an M-MMA coating floors can safely be returned to service on the same day and subjected to normal mechanical or chemical loads without incurring any negative consequences. This immediate return to service also effectively mitigates any direct or indirect financial risks related to production downtime.
Craft Flooring & Coatings is an accredited installer of
Plastifloor reactive resin coatings. Imported from Germany, Plastifloor is a tough and durable M-MMA flooring solution suited to a range of industries, from food processing and pharmaceutical facilities to light and heavy industrial plants, and each floor can be finished to satisfy the client’s requirement for colour and slip resistance.
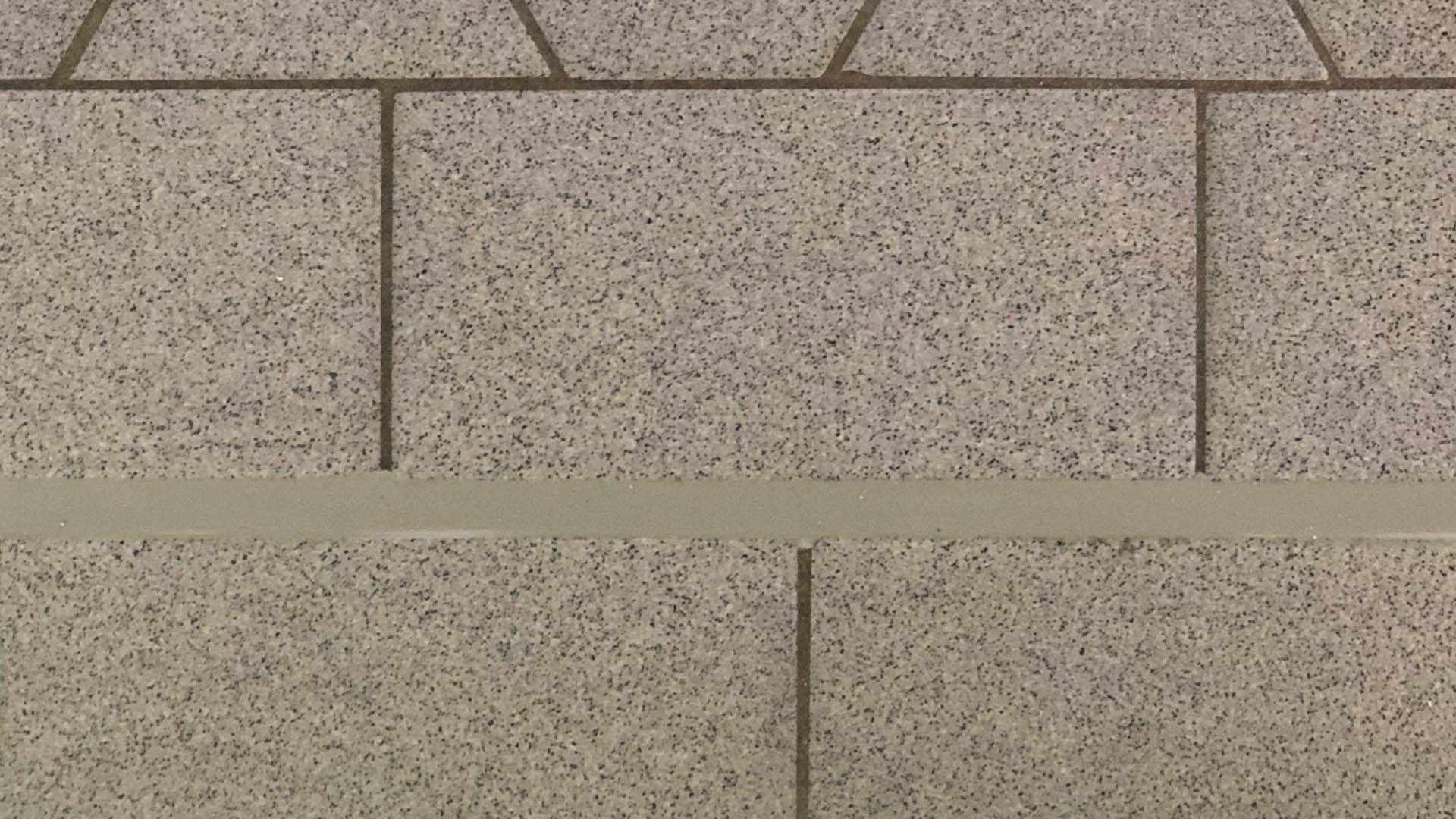
When repairing and installing floor joints without the guidance of architectural specifications or engineering drawings it may be tempting to disregard the need for proper joint care. However, not preparing the joints for the stresses it has to endure is a penny-wise pound-foolish approach that will almost surely result in floor failure.
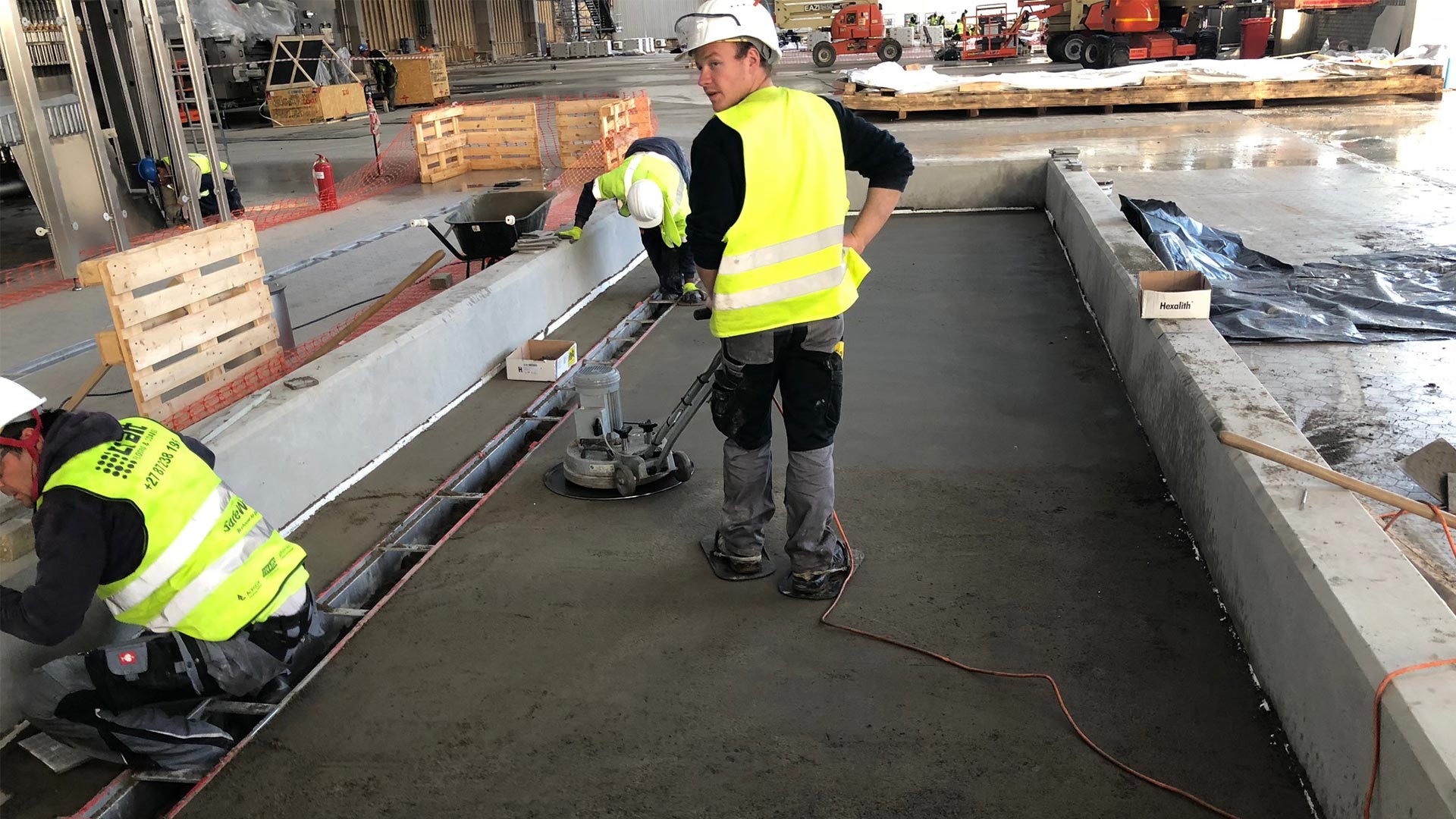
Commercial and manufacturing facilities understand the need for a well-designed, hygienic, durable, adaptable, cleanable, and serviceable drain system. Working closely with the engineering and production teams we can design a suitable full-service drain solution, commission the manufacture thereof, and then install the system in line with the specified requirements.
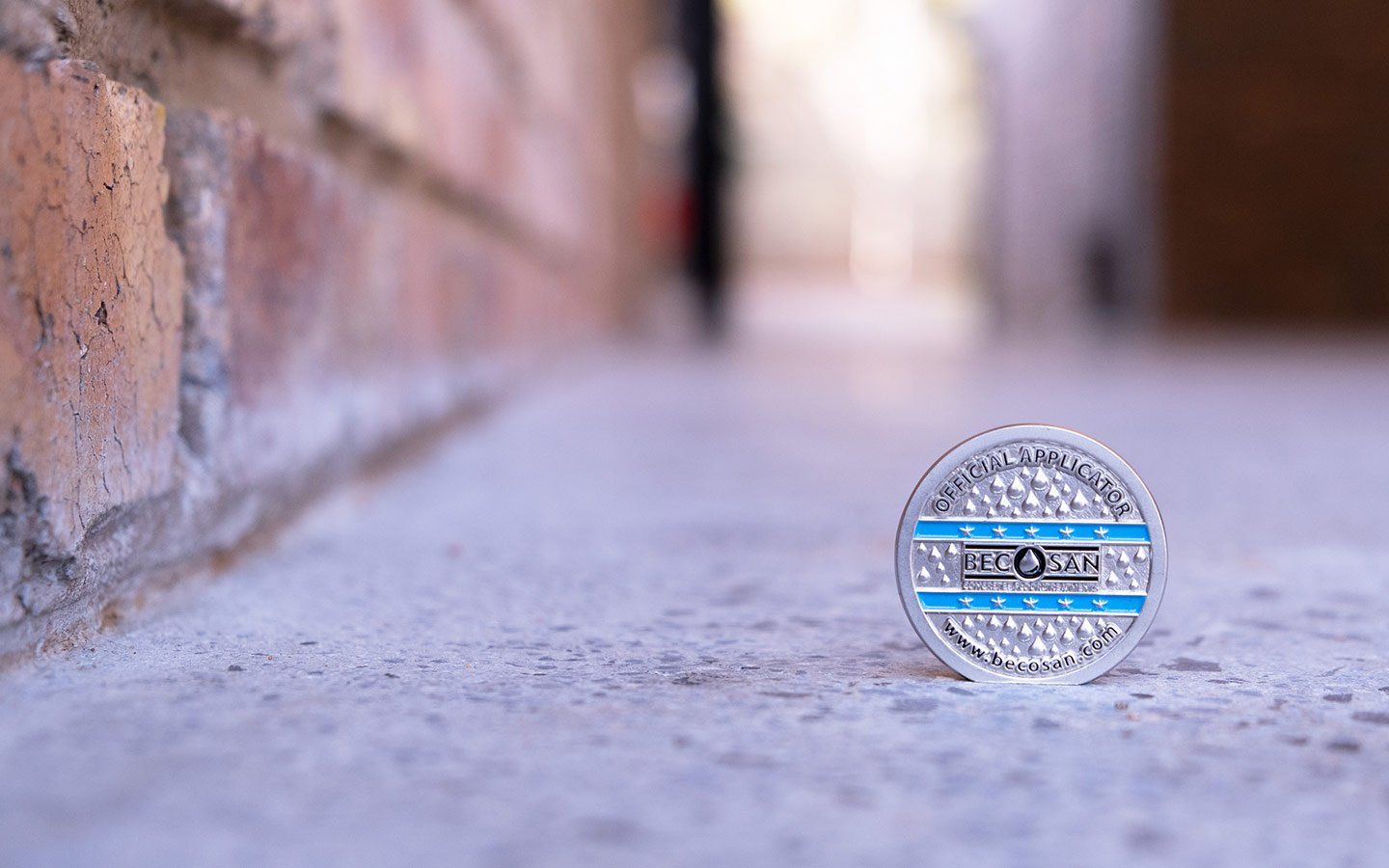
Craft Flooring & Coatings was approached by the owner of Venue 466 to assist with an unsightly delaminating floor covered with an epoxy coating that offered very little slip resistance. By treating the floor with Becosan’s non-film forming treatment the facility now boasts a beautiful non-slip, low maintenance concrete floor that will not delaminate.